Extrusion die drool is a common issue in the plastics industry that can cause a range of problems if not effectively managed. The problem arises when molten plastic material leaks from the extrusion die during the production process, leading to waste, product defects, and increased downtime for equipment cleaning. In this article, we will explore the causes of extrusion die drool and the steps that manufacturers can take to prevent it from occurring.
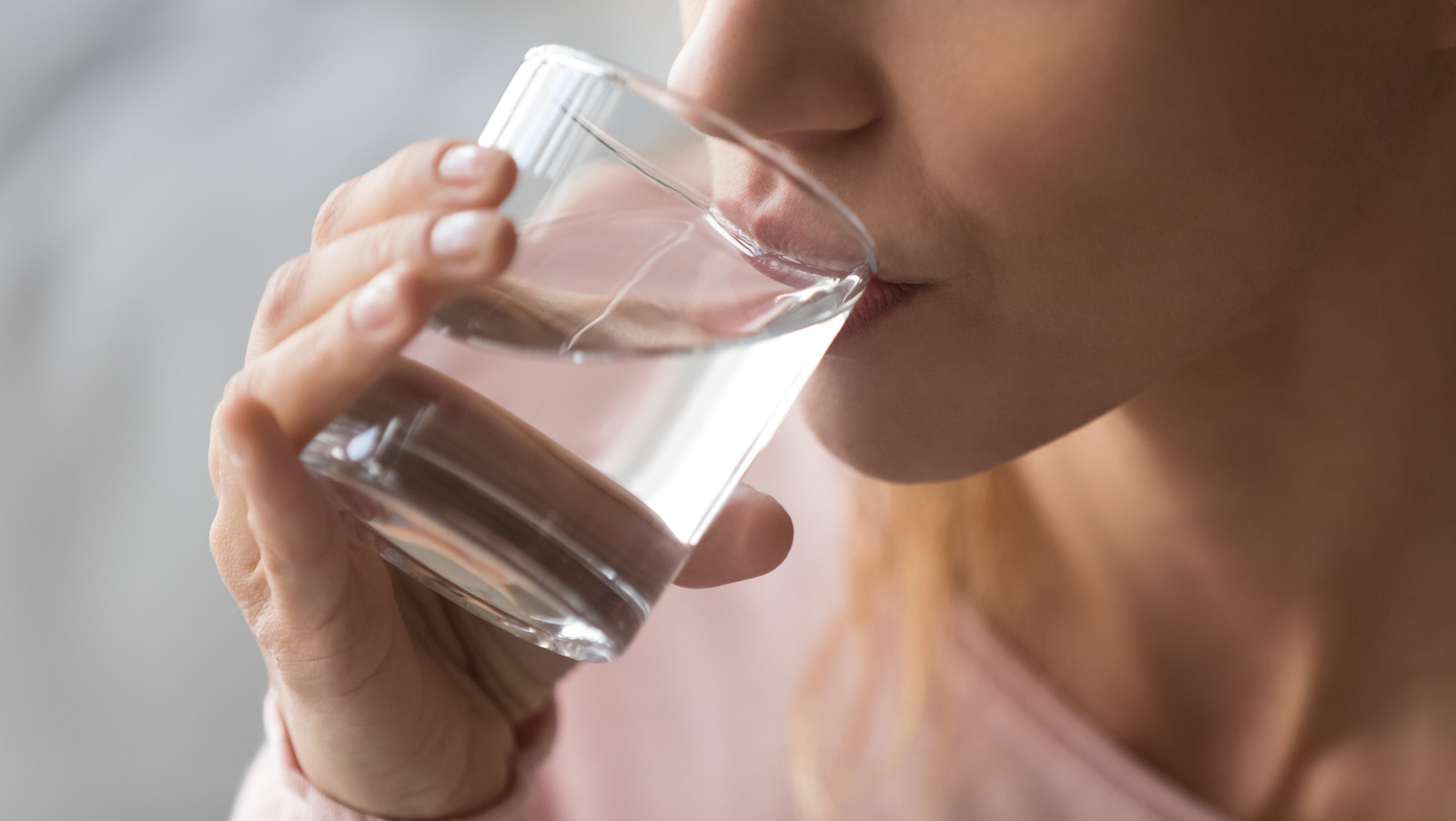
The first factor that contributes to extrusion die drool is the viscosity of the plastic material being processed. When the plastic has a high viscosity, it becomes increasingly difficult for the material to flow smoothly through the extrusion die. As a result, the material can build up and be forced out of the die in the form of drool. Typically, this problem occurs with high-molecular-weight polymer materials that are more difficult to process. To prevent this problem, manufacturers can reduce the viscosity of the plastic material by increasing the temperature of the extruder, increasing the screw speed, or reducing the die gap.
Another common cause of extrusion die drool is the design of the die itself. When the die is designed with too many or too few orifices, there can be differences in the pressure of the flow of the plastic material through the die. This differential pressure can lead to drool forming at the edges of the die as the material is forced through the orifices. Manufacturers can avoid this problem by designing and using dies that feature a uniform flow of material through all of the orifices.
Equipment maintenance is another crucial factor in preventing extrusion die drool. When the equipment is not adequately maintained or when it is experiencing wear and tear, the material can start to stick to the components of the die, leading to drooling. Manufacturers need to ensure that the equipment is regularly maintained, cleaned, and inspected to avoid any issues of wear and tear. It is also advisable to use high-quality equipment components to reduce the risk of such problems.
Another factor contributing to extrusion die drool is the process conditions. When the processing temperature is not optimal, the plastic material can become overheated or underheated, which can cause it to become sticky or sluggish, leading to drooling. Manufacturers need to ensure that the processing temperature, screw speed and pressure are all operating within the recommended ranges for their particular application. In addition, the cooling system of the extrusion line should also be properly designed and maintained to ensure that the cooling of the plastic material is done uniformly.
Finally, operators' practices can also affect the occurrence of extrusion die drool. When the operators are not correctly trained, they can sometimes unknowingly introduce errors into the process. For example, if they are using too much lubricant or if they are not cleaning the equipment properly, they can cause drooling. Operators must be trained on the proper handling and maintenance of the equipment, and they must adhere to established best practices to prevent any problems.
In conclusion, extrusion die drool is a common problem in the plastics industry that can lead to waste, product defects, and downtime. The main causes of the problem are the viscosity of the plastic, the design of the die, inadequate equipment maintenance, unfavorable process conditions, and the practices of the operators. To prevent this issue, manufacturers should take a holistic approach that considers all of these factors. By ensuring that the plastic material, the die design, the equipment maintenance, the process conditions, and the operator practices are all consistent with the production goals, manufacturers can significantly reduce the occurrence of extrusion die drool and minimize its impact on their operations.